Time to switch to recycled plastic
11 Oct 2019
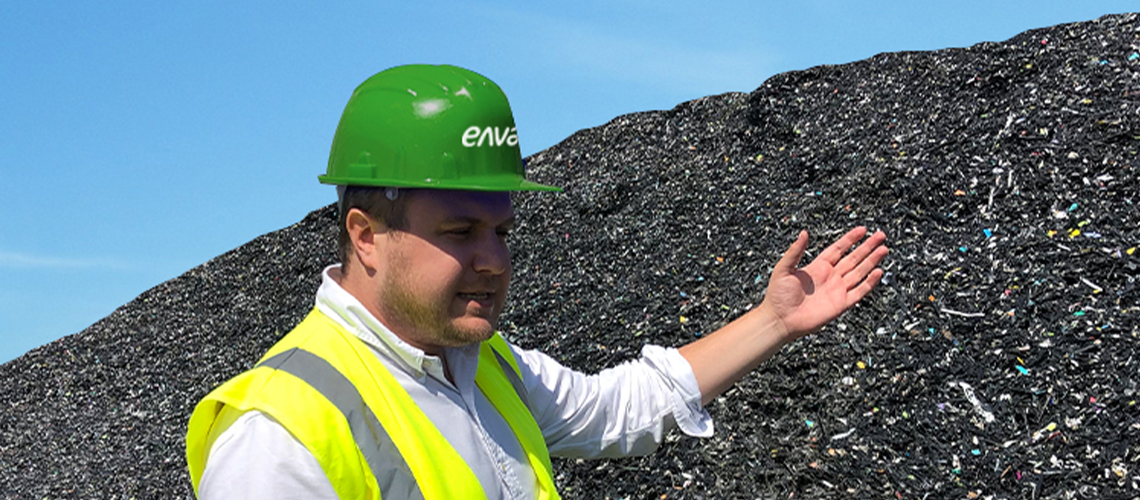
Steve Bell from Enva, one of the UK’s largest providers of recycled polymers, dispels some of the myths associated with incorporating recycled material into modern supply chains and points to the commercial and environmental benefits they can deliver UK and international manufacturers.
Since the impact that single use plastics were having on our oceans was first brought to our attention in 2017, forward thinking and proactive businesses have been developing ways to operate in a more sustainable manner. In doing so, they have been able to build a positive environmental element to their brand and create a valuable point of differentiation.
Whilst single use plastics have undoubtably been the focus of attention to date, there is certainly reason to be confident that this sentiment will broaden and that plastics will become increasingly demonised outside of just drinking straws, water bottles and carrier bags. There is also the potential that a tax similar to the government’s plastic packaging tax which will levy a charge on all plastic packaging with less than 30% recycled content, will be considered for other products.
The use of recycled plastics in manufacturing such as Polypropylene (PP), Acrylonitrile Butadiene Styrene (ABS) and Polystyrene (PS) got off to a difficult started in the 80’s and 90’s when they were generally manufactured in small scale, unsophisticated facilities and as a result, suffered from a high degree of contamination. This perception has proved hard to shift with many manufacturers including the automotive and white goods industries seemingly reluctant to incorporate these products into their processes.
The production of modern recycled polymers however has changed dramatically. Not only are they now comparable in terms of quality when compared to virgin oil-based products but they can also present users with a considerable cost saving. It’s also important to note that no modification of manufacturing equipment is required when offsetting virgin polymer for recycled meaning that there is no cost associated with the switch to a more sustainable supply chain.
Another historical concern with specifying recycled polymers for use in car manufacture, for example, was whether a product that was available today would still be available in say four years’ time. Long term production capability is no longer a restraining factor and indeed input materials are continually increasing as a result of an increasingly advanced waste and recycling sector. Enva alone has recently invested £1.8m in order to double its output capacity to over 2000 tonnes of extruded compound per month.
Variations to recycled polymers are also now far easier and economical. This could include the addition of elastomers to improve impact strength, additives to increase melt flow or fillers to make PP stronger and stiffer. A range of colours are also now available. In fact, it’s technically possible to produce any colour required by a customer.
Whilst there is little in the way of published data to assess the use of recycled polymers in the manufacture of modern goods, our experience indicates that take up remains far lower than would be expected given the commercial and environmental benefits. Phones, fridges or vacuum cleaners that promote a high percentage of recycled plastic as part of their marketing strategy cannot be too far away and this still presents a real opportunity for brands with the foresight to be early adopters of these high quality and valuable secondary resources.
| View all stories